Effective inventory management is a key element of productive construction projects. Effective inventory management is crucial for efficient project execution and cost management, from monitoring materials and supplies to making sure replenishment occurs on schedule.
Software for construction inventory management is useful in this situation. Construction organizations may improve resource use, increase efficiency, and streamline their inventory operations thanks to this strong tool. In this article, we delve into the realm of construction inventory management software, analyzing its advantages and how it is reshaping the sector.
Features of Construction Inventory Management Software
- Integration of barcode and RFID technology: Barcode and RFID (Radio Frequency Identification) technologies are frequently integrated into construction inventory management software. This speeds up and accurately scans goods, automates data input, and lowers human error rates. Items can be given barcodes or RFID tags for simple identification and tracking throughout the supply chain.
- Management of Material Requisitions and Purchase Orders: The program makes it possible to create and handle material requisitions and purchase orders. Purchase orders may be created, followed up on, and approved by project managers and site managers. This function makes sure that supplies are acquired on schedule, preventing delays and inventory shortages.
- Management of Vendors and Suppliers: Construction inventory management software makes it easier to handle vendors and suppliers effectively. It enables businesses to manage contracts and price agreements, keep an organized database of suppliers, monitor supplier performance, and simplify interactions with vendors. This function facilitates procurement process optimization and guarantees the prompt and trustworthy delivery of materials.
- Forecasting and Inventory Optimization: The program offers capabilities for forecasting and inventory optimization. The program can produce demand estimates and recommend ideal inventory levels by examining historical data, use trends, and project needs. This function lowers carrying costs, increases overall inventory management effectiveness, and helps minimize overstocking and stockouts.
- Mobile Accessibility: Several construction inventory management software packages have mobile apps that enable project teams and field employees to use cell phones or tablets to view inventory data. Since real-time updates, inventory requests, and progress tracking are all possible via mobile devices, communication and coordination between the office and the field are improved.
- Asset Tracking and Depreciation: Software for construction inventory management frequently includes asset tracking features for machinery and other expensive things. It enables businesses to monitor the asset’s history of use, location, and upkeep. Additionally, the program can compute asset depreciation, aiding businesses in efficiently managing the financial elements of their assets.
Benefits of Construction Inventory Management Software
- Effective Purchase and Replenishment: By giving insights into inventory levels, reorder points, and supplier information, the program streamlines and automates the purchase process. Construction organizations can create effective supplier relationships, negotiate better pricing, and make educated procurement decisions.
- Inventory monitoring and traceability: Materials can be tracked and traced throughout the supply chain thanks to construction inventory management software. Businesses may precisely track the whereabouts, transportation, and use of their materials by scanning barcodes or QR codes. This lowers the possibility of lost or missing inventory and simplifies logistics.
- Waste reduction and cost control are made possible by efficient inventory management software. Overstocking and unnecessary material purchases are reduced through accurate tracking of inventory levels and consumption. Construction businesses may dramatically save expenses and increase profitability by streamlining inventories and reducing waste.
- Resource Allocation Optimization: By enabling visibility into inventory availability across several sites, construction inventory management software supports effective resource allocation. Project managers may locate excess inventory and move it to locations where it is required, preventing duplication of purchases and maximizing resource use.
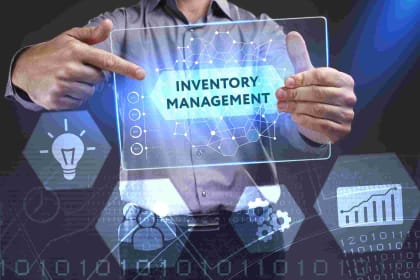
Disadvantages of Construction Inventory Management Software
- Construction inventory management software implementation often involves an initial expenditure in the form of software licensing, hardware infrastructure, and training. Small or cash-strapped construction firms could find it difficult to set aside money for the software’s deployment, which might slow down or prevent uptake.
- Learning Curve and Training: Employees who are not accustomed to using this type of software frequently have a learning curve while utilizing construction inventory management software. To guarantee that every user can efficiently browse and use the functionality of the program, adequate training and assistance may be required. The training procedure can take a lot of time and resources, which could interfere with regular business throughout the changeover.
- Data input Accuracy and Maintenance: For construction inventory management software to operate efficiently, accurate data input and continual data maintenance are required. erroneous data entry can result in erroneous inventory records and could influence decision-making processes. All users must be diligent and pay close attention to maintain data accuracy.
- Integration Problems: It might be difficult to integrate construction inventory management software with other systems, including accounting or project management software. Issues with compatibility, data migration, and maintaining smooth data transfer between systems could need technical know-how and extra resources. Ineffective system integration might result in inefficiencies, double data entry, or inconsistent data.
- Limited Flexibility and Customization: Construction inventory management software that is available off the market may not be as flexible or adaptable to different company processes or workflows. It may be difficult to fully configure the program to a company’s particular requirements if they have unusual requirements or sophisticated inventory management demands. This restriction could call for workarounds or concessions in some circumstances.
Conclusion
The way construction organizations manage their inventory, materials, and supplies is changing as a result of construction inventory management software. This program enables building companies to optimize their operations, minimize expenses, and enhance project results by boosting traceability, optimizing procurement and replenishment, and minimizing waste.